Bell Housing
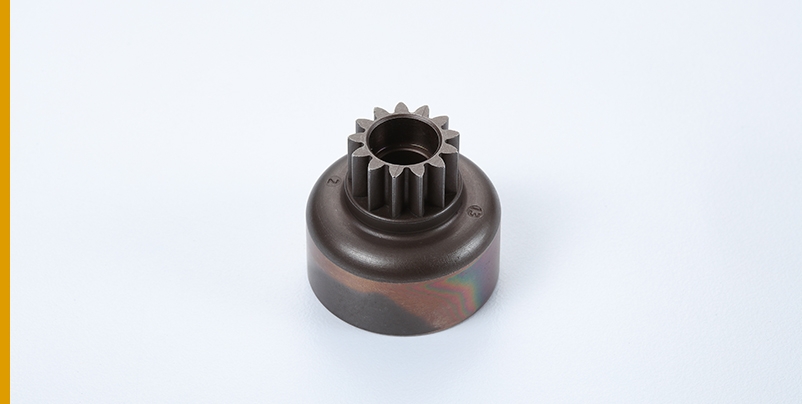
The diversity of manufacturing methods like metal powder injection molding has created the core competence of Jinholly and has become one of the important reasons why many clients choose Jinholly.
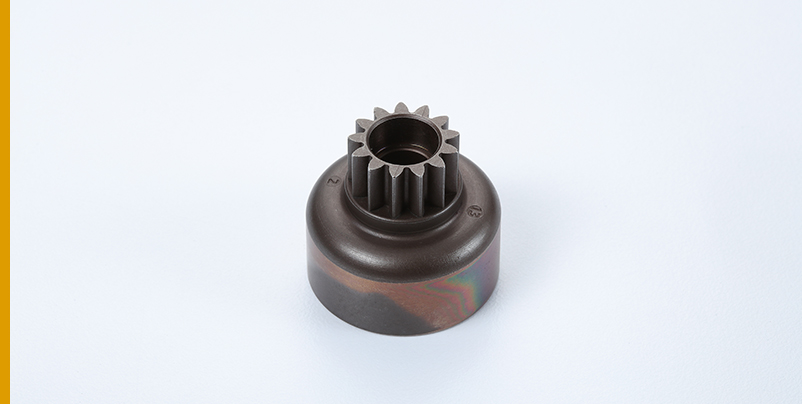
Solutions
The diversity of manufacturing methods has created the core competence of Jinholly and has become one of the important reasons why many clients choose Jinholly. We can understand it from the following case. The workpiece is a clutch cover/bell housing that drives the gear shaft and has the brake function inside a remote control car. Originally it was made by cutting iron bars, but the hobbing process required grooves that caused defects in material thickness, resulting in conflicts between acceleration and braking, leading to problems such as shortened life and breakage.
Evaluation of Workpiece
Suggested Method
After a long period of communication and coordination with the client to understand its functionality, we adopted metal powder injection, which changed the material conditions to improve the shortcoming of the groove and enhanced its strength and mechanical properties such as torque and toughness. After the endurance test and long-term running test with the client, we got significant results.
Ruggedisation
Benefit 1 : Enhance the torque and toughness of the workpiece.
Benefit 2 : Assist clients in solving complaints and enhance product durability.
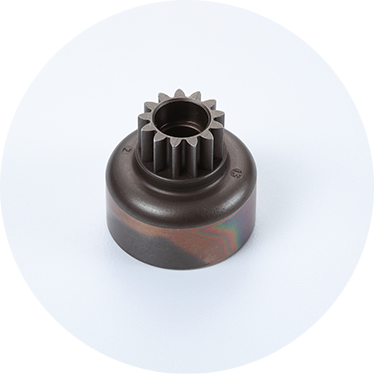
Final Generation
OEM / ODM Solution
Select appropriate processing methods for clients to help them reduce costs, achieve high efficiency, and high-quality service.